According to specialists, using aluminum may make civil construction and the automotive industry more sustainable
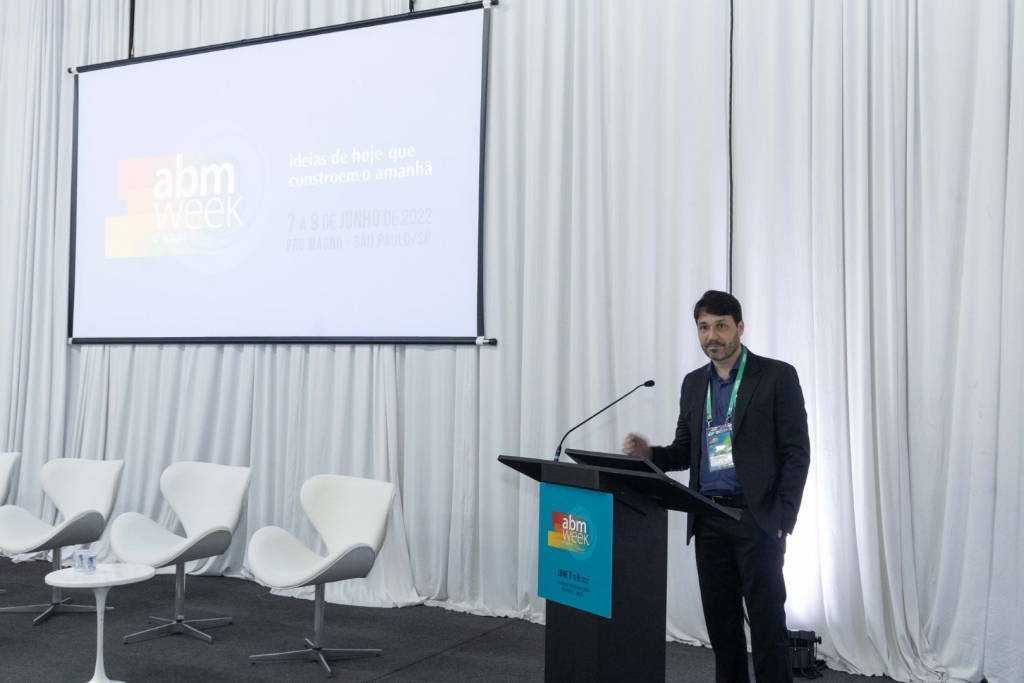
The relationship between the use of aluminum and sustainability in civil construction and the automotive industry was discussed during the Aluminum and Sustainability as Market Drivers panel held on June 9 (Wednesday) during the 6th edition of ABM WEEK.
Magda Reis, a consultant for ABAL (Brazilian Aluminum Association), was the civil construction panel moderator. The first lecture addressed the role played by aluminum in rising energy efficiency and was presented by Maíra Macedo, project and certification manager with GBC (Green Building Council Brazil). “The energy aspect is a major component in the certification process and an aluminum façade leads to significant energy consumption reductions. Aluminum has a positive effect on the façade and may also be used as a sealing element and in the frames to reduce the thermal transmittance,” Macedo explains.
Next, Paulo Gentile, Hydro's product development coordinator, spoke about aluminum-built construction components, particularly windows and doors. Heat transmission can be blocked through very efficient systems, such as polyamide bars and shapes. “I just visited Argentina in early May and orders for this material will be placed in March; there is a lot of demand for this solution,” says Gentile. These products meet and even exceed the parameters set out by Performance (NBR 15.575) and Building Frames (NBR 10.821) standards.
André Cardoso, commercial consultant at CBA, recalled that steel, in addition to being used in all construction phases, finds excellent applications as a connecting element between different materials: glass, concrete, stainless steel, polymers, and others. “Aluminum’s main advantage is in connecting systems. You can design it without adaptations,” he stresses.
Last but not least, Lucínio Abrantes and Lúcio Abrantes presented their manufacturing experience by describing cases in which their company, Luxalum, was involved, including aluminum frames, special façades, unitized system, photovoltaic façades, and other solutions. The company is present in many Triple A projects in Brazil. “The industry’s trend focuses on efficient projects using high-performance insulated glass.”
More sustainable vehicles
The automotive industry panel was moderated by Ana Paola Villalva Braga, materials engineer at IPT (Technological Research Institute). The first lecturer was Carolina Hattori, market development and innovation consultant with CBA, who spoke about research into new alloys for use in structural components – pedestrian protection, luggage racks, tunnel brace, and door protection bar.
“In the energy-related study, we reduced the part weight by 2.7 times, whereas the weight-related study showed that the absorption of impact energy was increased by six times when compared to steel,” Hattori says.
Another lecturer, Oliver Toríbio, metallurgical engineer at Novelis, pointed out the increasing use of aluminum in automobiles year in, year out, but noted that, while the average weight of aluminum per car is 60 kg in Brazil, it is 180 kg in the U.S..
In one of his studies, he compared an all-steel car body, whose total weight would be 270 kg, with another that heavily uses aluminum, resulting in a weight of 190 kg (a 30% reduction), and yet delivered equal or better performance in crash tests. “For every 10 kg reduction in car weight, there’s an efficiency gain from 5% to 7%; and for every kilogram of steel that is replaced by aluminum, CO2 emissions drop by 13 kg to 20 kg,” Toribio explains.
The third and last speaker, Guilherme Fernandes, engineering manager with Stellantis, discussed the growing use of aluminum in other car parts, such as the body, and said this is a step Brazil and Latin America should take in the coming years.
The 6th ABM WEEK is hosted by Gerdau and is sponsored by the following companies: Açokorte, Alkegen, Amepa GmbH, Aperam, ArcelorMittal, Atomat Services, AutoForm, BM Group/Polytec,BRC, BR Event Materials ,CBMM, Combustol, Clariant, Danieli, Dassault Systèmes, DME Engenharia, Eirich, Enacom, Engineering, Evonik, Fosbel, GSI, Harsco, Hatch/CISDI, Ibar, Imerys, IMS Messsysteme GmbH, Isra Vision Parsytec, John Cockerill Industry, Kuttner, Metso Outotec, Nalco Water/Ecolab, Nouryon, Primetals Technologies, PSI Metals, Reframax , RHI Magnesita, Saint-Gobain, SMS Group Paul Wurth/ Vetta, Spraying Systems, Suez, SunCoke, Tecnosulfur, Ternium, Timken, Thermo Fischer, TopSolid, TRB, Unimetal, Usiminas, Vale, Vamtec, Vesuvius, Villares Metals, Wallonia.be (ADI – Industrial Services, John Cockerill Hydrogen, BorderSystem, Datanet International, Synthetis e PEPITe), White Martins, e Yellow Solution.Special support: CNPq. Institutional support: Abal, Abendi, Abifa, AIST, AIST Mena, Alacero, CBCA, Ibram, Icz, Instituto Aço Brasil, CIMM, Ind4.0.
Deixe seu comentário